Two Hyundai crawler excavators in heavy-duty sewer construction
Dauberschmidt-Gruppe is based in the German town of Dinkelsbühl. With a history dating back 130 years, this family-owned company, headed by managing director Peter Kehrle, is active in above ground, below ground and industrial construction, turnkey prefabricated construction and the sale of building materials in the Middle Franconia region of Bavaria. For about a year, two Hyundai crawler excavators have been in operation as part of the roughly 50-strong fleet of excavators and wheel loaders – one R235LCR-9 and, since mid-2019, one heavy-duty 30 metric ton HX300L. These machines, which are currently predominantly involved in sewer construction, are managed by the authorised HCEE dealer Engelhardt Baumaschinen GmbH from Schopfloch.
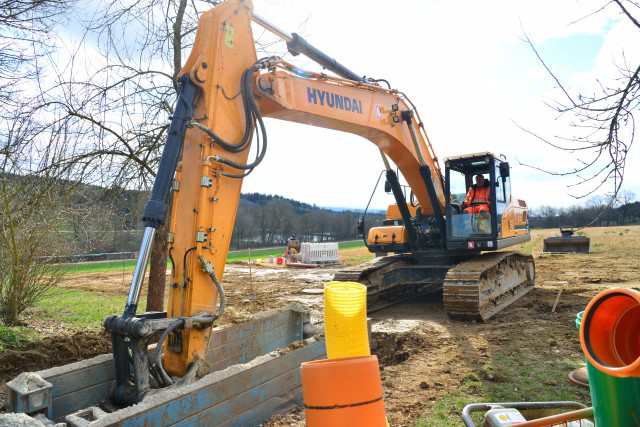
A major construction project for renewal of the complete sewer system in Dinkelsbühl-Sinbronn has been underway since mid-2018. Within two years, 6,000 metres of new sewers with open channel design will be laid (Dauberschmidt is a member of the sewer quality association Gütegemeinschaft Kanalbau) and approximately 140 house connections will be replaced. DN 200 plastic pipes are being used for this project. The range of services required during sewer construction includes the manufacture and installation of pressure pipelines right up to the gas and water lines. In addition, containers, special structures and reservoirs must be built, along with commercial buildings and outdoor installations.
The new pipes are laid at depths of 3,000 to 6,000 mm. To achieve this, 12,000 m³ of excavated materials must be moved. This is time-consuming work as the excavated materials must be hauled away by truck, only to be brought back again for backfilling once the lines have been laid. Separate pipelines for rainwater and service water are being laid.
Latest excavator technology
The 35 metric ton, heavy-duty HX300LR is equipped with a 10,200 mm long boom and 7,850 mm long arm. 800 mm triple grouser track shoes ensure secure footing. The 14,560 mm long and 35,000 kg excavator is ready for action, and can be easily transported as an undivided load by means of a low loader.
A maximum reach of 19,000 mm makes the HX300LR ideal for embankment and sewer work, demolition work, and large earthworks. With the HX series (14 to 90 metric ton application weights), Hyundai Construction Equipment Europe introduces a newly designed range of modern, ergonomic and high performance hydraulic excavators. Stage IV engine from Perkins, Cummins and Scania, a new design, and extensive new and further developments in the cabin, components and operation are attractive selling points. An important feature of all HX hydraulic excavators is the interior, which is up to four dB quieter, and cabin, which is now 13% larger. It is a defining design element and gives the HX machines a distinctive look with a high recognition value.
The capacitive touchscreen display has been enlarged to 8 inches. The operator can use the display to make numerous parameter settings in clear and intuitive menu items. Two views and three modes are available. In addition to displays and switches, many settings can be made very easily using superimposed sliders and adjusted with minimal effort. There are also 18 conventional buttons under the display for activating central lubrication, idle throttle, work lights, etc. The responsive display is glare-free, low-vibration and can be freely adjusted in inclination and direction of rotation.
Moreover, information can be transferred from a smartphone directly to the display via WiFi. To make it easier for the operator to work efficiently, the display has a large, colour ECO display. Coloured bars in the tachometer indicate efficiency – green bars indicate efficient operation, red represent high fuel consumption and wear. Three operating modes – ECO, Standard and Power – are stored in the control and can be selected.
Depending on the function selected, the knob reacts differently to physical feedback. The radio is integrated in the right-hand armrest, in direct reach of the operator. It is equipped with a Bluetooth and USB interface for connecting a smartphone and radio. The standard microphone is synchronised with the hands-free system via the Bluetooth feature of the radio. To make it easier for the operator to work efficiently, the display has a colour ECO display. Coloured bars in the tachometer indicate efficiency – green bars indicate efficient operation, red represent high fuel consumption and wear. Three operating modes – ECO, Standard and Power – are stored in the control and can be selected by pressing a button.
The main focus of further development work is the operator and their demands for comfort and safety. The new ROPS/FOPS cabin is mounted on especially well-insulated dampers, significantly reducing the vibrations at the operator seat. The operator seat and control panels with joysticks are a single unit that automatically adjust to the operator's weight.
The oil quantity and pressure of up to 20 attachments can be stored in a directory via the touchscreen (Hyundai calls this the EPPR function – the Electronic Proportional Pressure Reducing valve function). For particularly demanding attachments, the hydraulic delivery rate can be increased by connecting two pumps together. This configuration data is also stored in the Hyundai system together with the pressure and oil delivery quantity. This feature is particularly important in demolition, where there is always switching between hammer, scissors, pulveriser, sorting bucket, etc.
Safety is a top priority for Hyundai products. The reversing camera is fitted as standard. As an option, Hyundai offers the AAVM (Advanced Around View Monitoring) system, which presents a 360-degree all-round view, compiled from the image information of four cameras mounted on the excavator, on the display. With the with the IMOD (Intelligent Moving Objects Detection) monitoring system that is also available, objects moving in the vicinity of the excavator are detected and presented on the touchscreen display.